Basement Flooring Options for Rhode Island's Climate
The best basement flooring options for Rhode Island's climate are luxury vinyl plank (LVP), polished concrete, ceramic tile, and engineered hardwood with proper moisture barriers. Rhode Island's humid summers, cold winters, and coastal moisture require flooring that resists water damage, handles temperature fluctuations, and provides comfort in below-grade spaces throughout the Ocean State.
Why Rhode Island's Climate Demands Special Flooring Considerations
Rhode Island's unique coastal climate creates specific challenges for basement flooring. The state experiences humid summers with high moisture levels, cold winters with potential freeze-thaw cycles, and year-round coastal humidity that can penetrate below-grade spaces in Providence, Newport, Warwick, and throughout the Ocean State.
Climate Factors Affecting Basement Flooring
High Humidity Levels:
- Summer humidity often exceeds 70%
- Coastal moisture infiltration
- Condensation on cool basement surfaces
- Mold and mildew growth potential
Temperature Fluctuations:
- Winter temperatures below freezing
- Summer heat and humidity
- Thermal expansion and contraction
- Seasonal moisture level changes
Coastal Moisture:
- Salt air infiltration
- Groundwater table variations
- Storm surge potential in coastal areas
- Increased corrosion and moisture damage
Top Basement Flooring Options for Rhode Island
1. Luxury Vinyl Plank (LVP) - Best Overall Choice
Why LVP Works for Rhode Island:
- 100% waterproof core construction
- Handles temperature fluctuations well
- Comfortable underfoot in cold basements
- Available in wood and stone looks
Cost: $3-$8 per square foot installed
Lifespan: 15-25 years
Maintenance: Low - sweep and mop regularly
Pros:
- Completely waterproof
- Easy installation over concrete
- Warm and comfortable feel
- Excellent durability
- Wide variety of styles
Cons:
- Can be damaged by heavy furniture
- May fade in direct sunlight
- Not as premium as real wood
Best For: Family rooms, bedrooms, offices, and high-traffic areas
2. Polished Concrete - Most Durable Option
Why Polished Concrete Suits Rhode Island:
- Naturally moisture-resistant
- Handles temperature changes excellently
- Won't support mold or mildew growth
- Integrates well with radiant heating
Cost: $5-$12 per square foot installed
Lifespan: 50+ years
Maintenance: Very low - periodic resealing
Pros:
- Extremely durable and long-lasting
- Moisture and mold resistant
- Modern, industrial appearance
- Works with radiant floor heating
- Eco-friendly option
Cons:
- Can be cold underfoot
- Hard surface (fatigue-inducing)
- Limited design options
- Requires professional installation
Best For: Modern basements, workshops, and contemporary designs
3. Ceramic and Porcelain Tile - Premium Water Resistance
Why Tile Excels in Rhode Island Basements:
- Completely waterproof when properly installed
- Unaffected by humidity changes
- Easy to clean and maintain
- Excellent for radiant heating systems
Cost: $4-$10 per square foot installed
Lifespan: 20-30 years
Maintenance: Low - regular cleaning and periodic grout sealing
Pros:
- 100% waterproof
- Huge variety of styles and colors
- Easy to clean and maintain
- Excellent durability
- Works with radiant heating
Cons:
- Cold and hard underfoot
- Can crack if substrate moves
- Grout lines require maintenance
- More expensive installation
Best For: Bathrooms, laundry rooms, and high-moisture areas
4. Engineered Hardwood - Premium Appearance
Why Engineered Wood Can Work in Rhode Island:
- More stable than solid wood
- Moisture-resistant with proper installation
- Adds significant value to homes
- Comfortable and warm appearance
Cost: $6-$12 per square foot installed
Lifespan: 15-20 years in basements
Maintenance: Medium - periodic refinishing
Pros:
- Premium appearance and feel
- Adds significant home value
- Can be refinished
- Comfortable underfoot
- Many style options
Cons:
- Requires excellent moisture control
- More expensive than alternatives
- Can be damaged by water
- Needs proper acclimation
Best For: Finished basements with excellent moisture control
5. Rubber Flooring - Comfort and Safety
Why Rubber Works for Rhode Island:
- Naturally water-resistant
- Provides cushioning and warmth
- Excellent slip resistance
- Handles temperature changes well
Cost: $3-$7 per square foot installed
Lifespan: 10-20 years
Maintenance: Low - regular cleaning
Pros:
- Comfortable and warm underfoot
- Excellent slip resistance
- Water and moisture resistant
- Good for exercise areas
- Easy to install
Cons:
- Limited aesthetic appeal
- Can retain odors
- May not add home value
- Industrial appearance
Best For: Home gyms, playrooms, and utility areas
Flooring Options to Avoid in Rhode Island Basements
Solid Hardwood
Why It's Problematic:
- Highly susceptible to moisture damage
- Expands and contracts with humidity
- Expensive to replace when damaged
- Doesn't meet most building codes for basements
Laminate Flooring
Major Issues:
- Swells and warps when wet
- Cannot be refinished if damaged
- Moisture destroys the core material
- Not waterproof despite marketing claims
Carpet
Significant Problems:
- Retains moisture and odors
- Supports mold and mildew growth
- Difficult to clean thoroughly
- Becomes health hazard when wet
Moisture Control Requirements for All Flooring Types
Basement Moisture Testing
Humidity Levels:
- Ideal range: 30-50% relative humidity
- Maximum acceptable: 60% relative humidity
- Test with digital hygrometer
- Monitor seasonally for variations
Concrete Moisture Testing:
- Plastic sheet test for 24 hours
- Concrete moisture meter readings
- Calcium chloride test for precise measurements
- Professional testing recommended
Essential Moisture Control Systems
Dehumidification:
- Whole-house dehumidifiers
- Portable units for smaller spaces
- Automatic drainage systems
- Humidity monitoring controls
Vapor Barriers:
- 6-mil plastic sheeting minimum
- Sealed seams and edges
- Proper installation under flooring
- Integration with wall vapor barriers
Drainage Systems:
- Interior perimeter drains
- Sump pump systems
- Exterior foundation drainage
- Proper grading around foundation
Subfloor Systems for Rhode Island Basements
Concrete Subfloor Preparation
Moisture Sealing:
- Epoxy moisture sealers
- Polyurethane coatings
- Penetrating sealers
- Vapor barrier installation
Leveling Requirements:
- Self-leveling compounds
- Grinding high spots
- Filling cracks and voids
- Professional assessment
Raised Subfloor Systems
Benefits for Rhode Island:
- Air circulation beneath flooring
- Insulation layer for warmth
- Moisture barrier integration
- Easy access for repairs
Material Options:
- Plywood over sleepers
- Engineered subfloor panels
- Foam insulation boards
- Combination systems
Cost: $2-$5 per square foot additional
Installation Considerations for Rhode Island
Seasonal Timing
Best Installation Times:
- Late spring through early fall
- Avoid high humidity periods
- Allow for material acclimation
- Consider heating system operation
Material Acclimation:
- Bring materials to basement temperature
- Allow 48-72 hours for adjustment
- Maintain consistent temperature
- Monitor humidity levels
Professional vs. DIY Installation
DIY-Friendly Options:
- Luxury vinyl plank with click-lock
- Rubber tiles and planks
- Some ceramic tile projects
- Painted concrete sealing
Professional Installation Required:
- Polished concrete systems
- Complex tile installations
- Engineered hardwood
- Moisture control systems
Cost Analysis for Rhode Island Basement Flooring
Total Project Costs (800 sq ft basement)
Luxury Vinyl Plank:
- Materials: $2,400-$4,800
- Installation: $1,600-$2,400
- Total: $4,000-$7,200
Polished Concrete:
- Materials: $1,600-$3,200
- Installation: $2,400-$6,400
- Total: $4,000-$9,600
Ceramic Tile:
- Materials: $2,000-$4,000
- Installation: $2,400-$4,800
- Total: $4,400-$8,800
Engineered Hardwood:
- Materials: $3,200-$6,400
- Installation: $1,600-$3,200
- Total: $4,800-$9,600
Additional Costs to Consider
Subfloor Preparation: $1,600-$4,000
Moisture Control Systems: $2,400-$6,400
Permits and Inspections: $200-$800
Trim and Transitions: $400-$1,200
Maintenance Requirements by Flooring Type
Luxury Vinyl Plank
Daily: Sweep or vacuum debris
Weekly: Damp mop with mild cleaner
Monthly: Deep clean with manufacturer's cleaner
Annually: Inspect for damage and wear
Polished Concrete
Daily: Sweep or dust mop
Weekly: Mop with pH-neutral cleaner
Annually: Reapply sealer as needed
Every 5-10 years: Professional re-polishing
Ceramic Tile
Daily: Sweep or vacuum
Weekly: Mop with tile cleaner
Monthly: Clean grout lines
Annually: Reseal grout
Engineered Hardwood
Daily: Sweep or vacuum
Weekly: Damp mop with wood floor cleaner
Monthly: Inspect for moisture damage
Every 5-10 years: Professional refinishing
Special Considerations for Coastal Rhode Island Properties
Salt Air Protection
Corrosion Prevention:
- Stainless steel fasteners
- Aluminum or composite trim
- Protective coatings on metal
- Regular inspection schedule
Moisture Management:
- Enhanced dehumidification
- Improved ventilation systems
- Frequent humidity monitoring
- Preventive maintenance programs
Flood Zone Considerations
Flood-Resistant Materials:
- Closed-cell foam products
- Inorganic materials preferred
- Quick-drying options
- Easy-to-clean surfaces
Elevation Requirements:
- Compliance with flood zone regulations
- Proper drainage systems
- Sump pump backup systems
- Insurance considerations
Energy Efficiency and Comfort
Insulation Integration
Under-Floor Insulation:
- Rigid foam boards
- Spray foam applications
- Reflective barriers
- Thermal breaks
Radiant Heating Systems:
- Electric radiant mats
- Hydronic radiant systems
- Thermostat controls
- Energy efficiency benefits
Comfort Enhancements
Area Rugs and Mats:
- Washable options preferred
- Moisture-resistant backing
- Strategic placement
- Seasonal rotation
Air Circulation:
- Ceiling fans for air movement
- HVAC system integration
- Natural ventilation when possible
- Humidity control systems
Building Code Compliance in Rhode Island
Flooring Requirements
Habitable Spaces:
- Moisture-resistant materials required
- Proper vapor barriers
- Ventilation compliance
- Egress accessibility
Bathroom Areas:
- Waterproof flooring mandatory
- Proper slope for drainage
- Non-slip surfaces required
- Ventilation system integration
Permit Requirements
When Permits Are Needed:
- Major flooring system changes
- Electrical work for radiant heating
- Plumbing modifications
- Structural subfloor changes
Inspection Process:
- Plan review and approval
- Rough-in inspections
- Final flooring inspection
- Certificate of occupancy
Return on Investment by Flooring Type
Resale Value Impact
Luxury Vinyl Plank:
- Moderate value increase
- Broad market appeal
- Low maintenance attracts buyers
- 60-70% cost recovery
Polished Concrete:
- Higher-end market appeal
- Durability valued by buyers
- Modern aesthetic attracts millennials
- 70-80% cost recovery
Ceramic Tile:
- Premium appearance valued
- Durability and low maintenance
- Classic appeal to most buyers
- 70-85% cost recovery
Engineered Hardwood:
- Highest value addition
- Premium market appeal
- Significant home value increase
- 80-90% cost recovery
Ready to install the perfect basement flooring for your Rhode Island home? Rockhouse Construction specializes in basement flooring installations that stand up to the Ocean State's challenging climate. Our experienced team understands moisture control requirements, proper subfloor preparation, and the best materials for Rhode Island's coastal environment. From luxury vinyl plank to polished concrete, we'll help you choose and install flooring that combines beauty, durability, and value. Contact us today for a consultation and estimate on your basement flooring project.
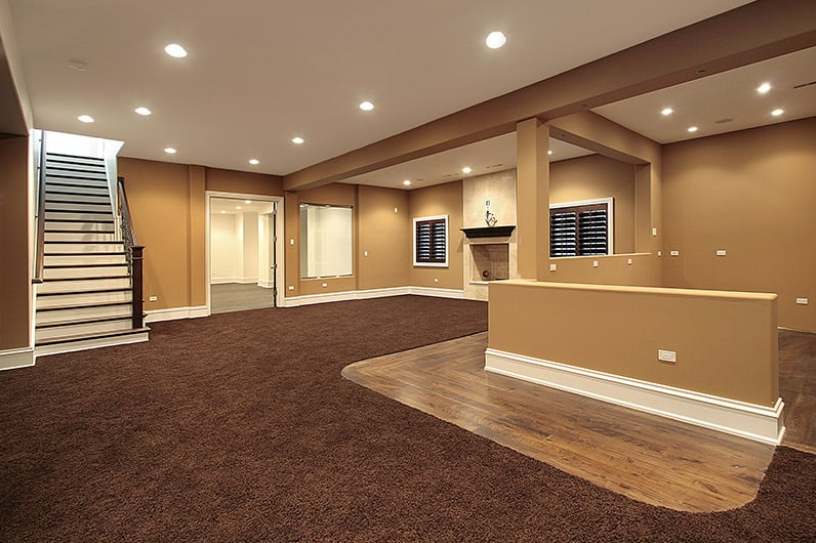
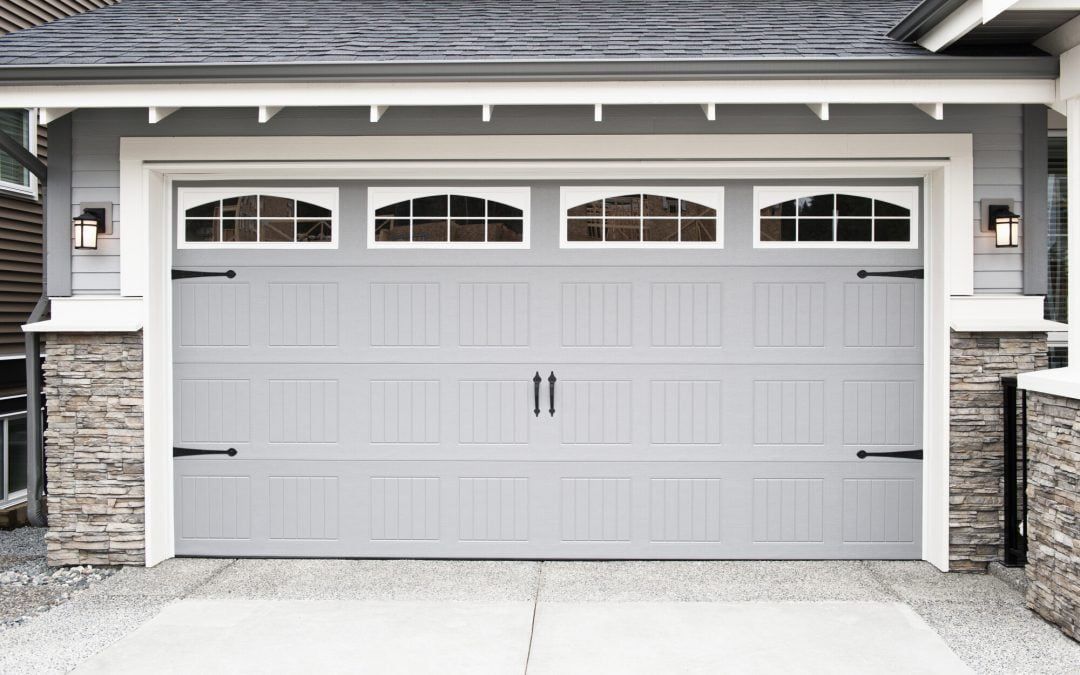
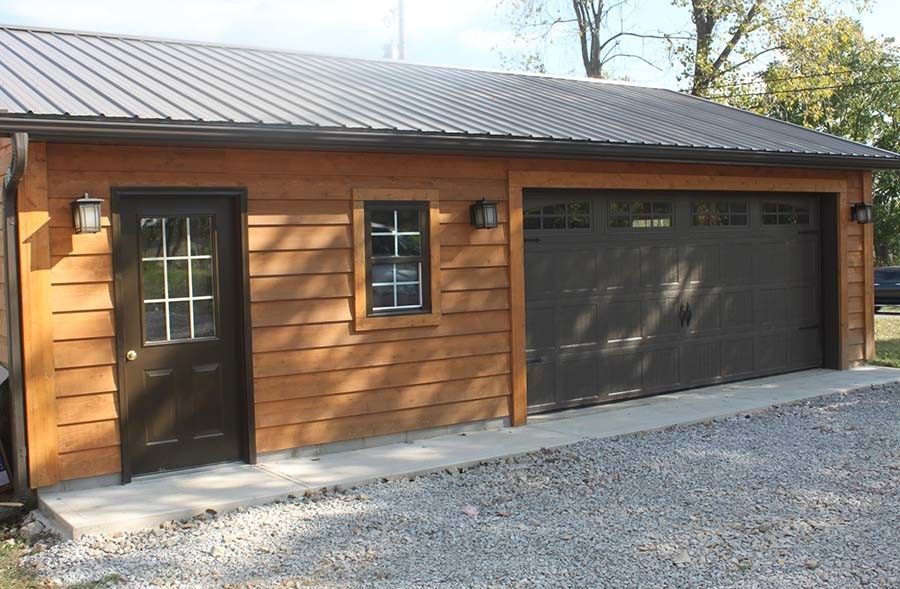
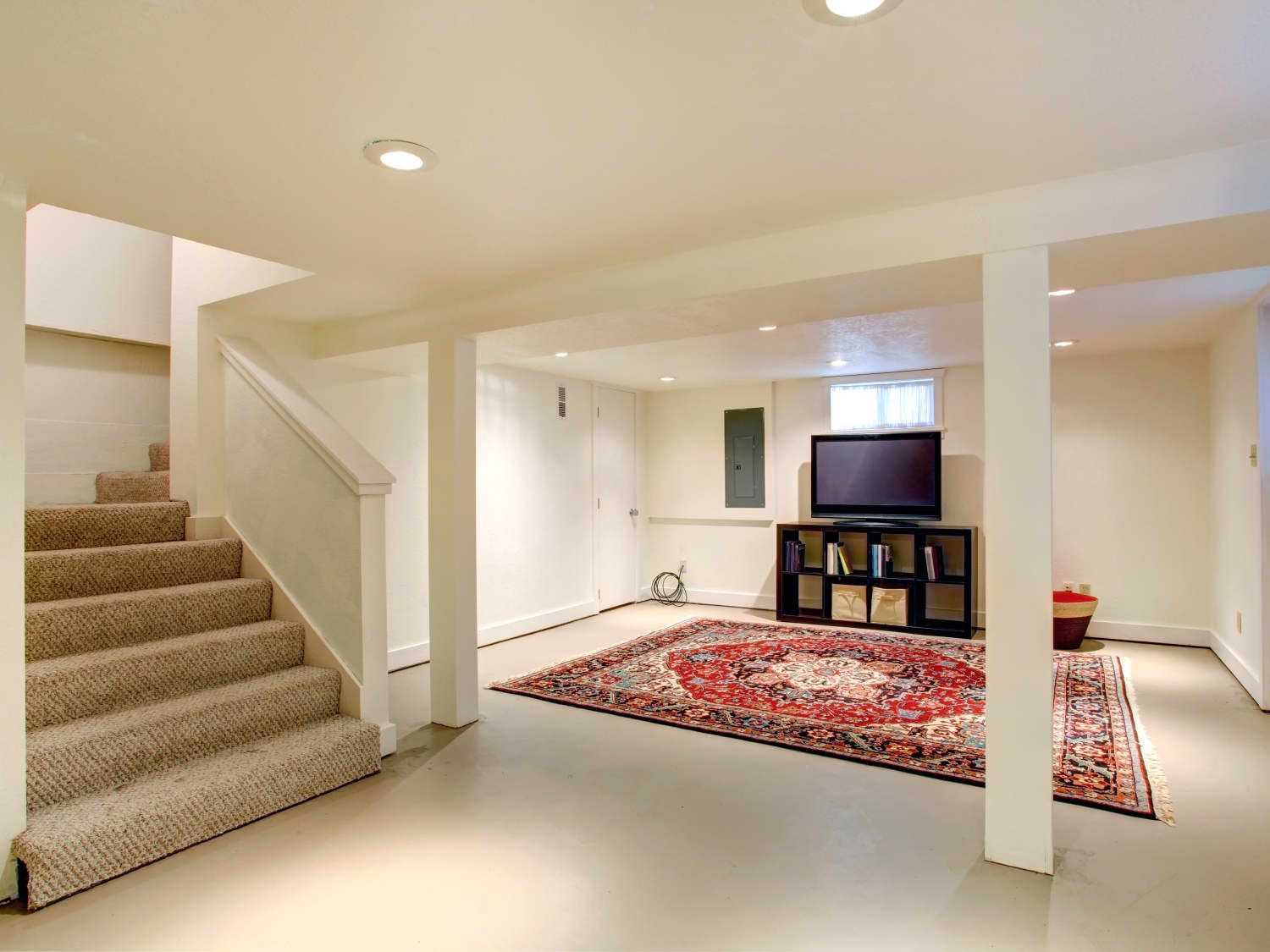
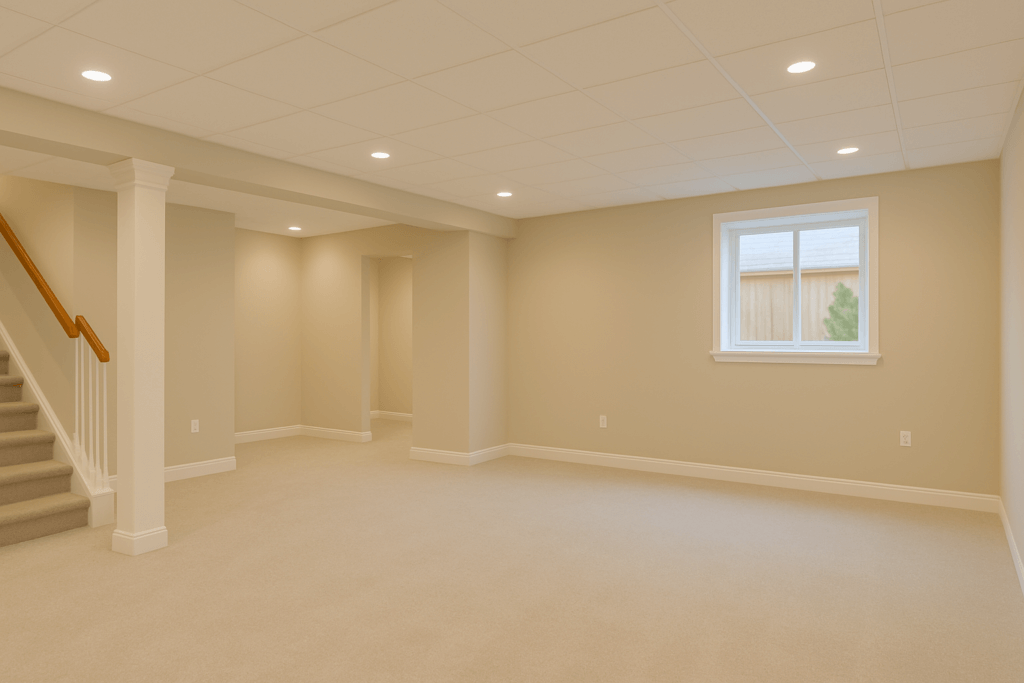
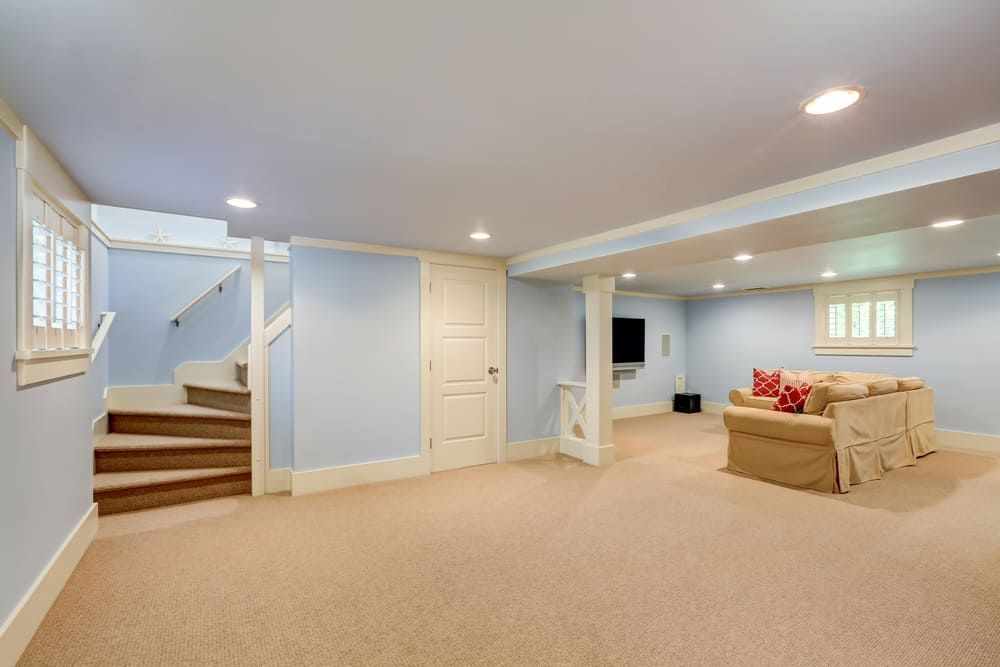
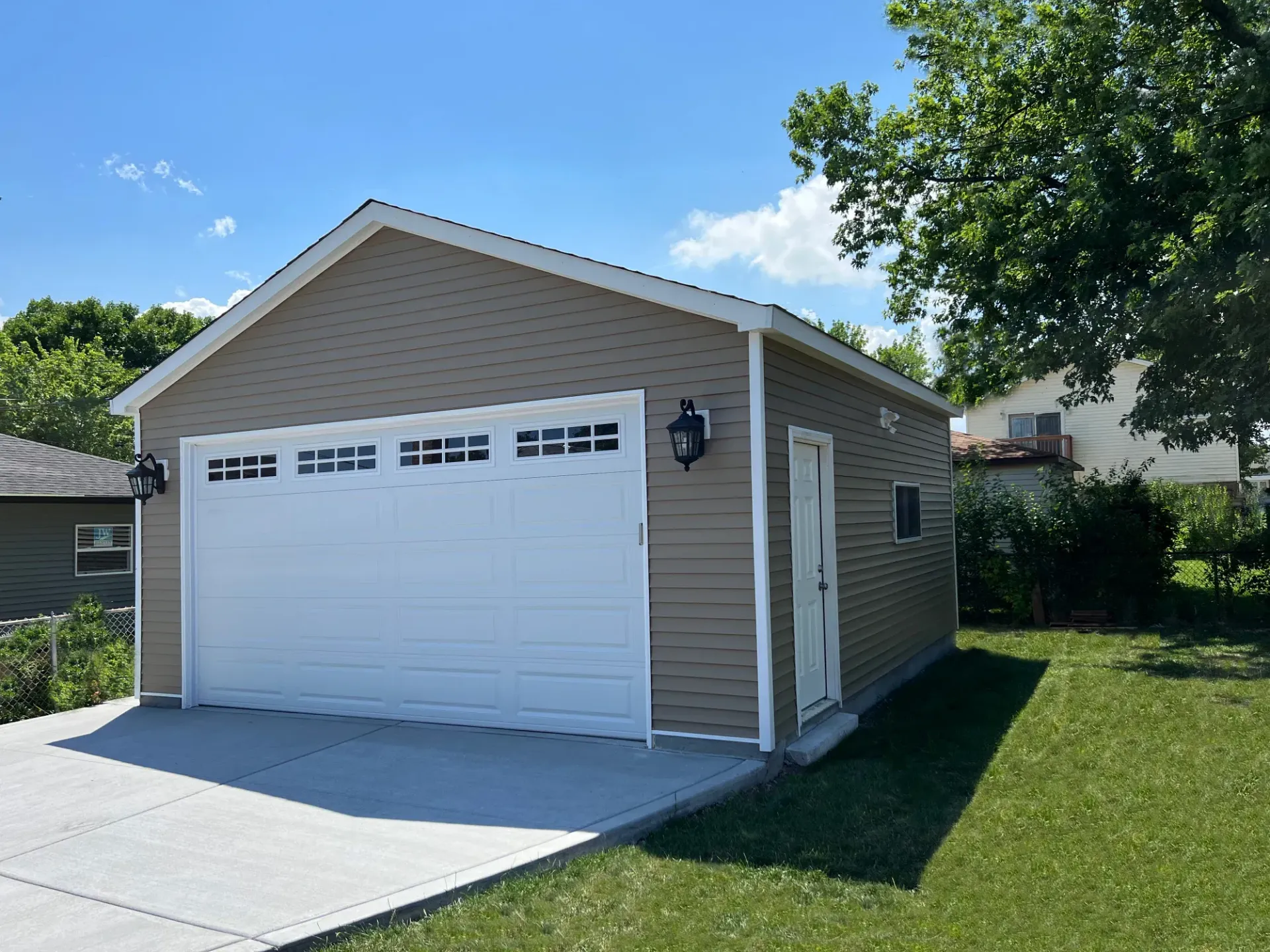
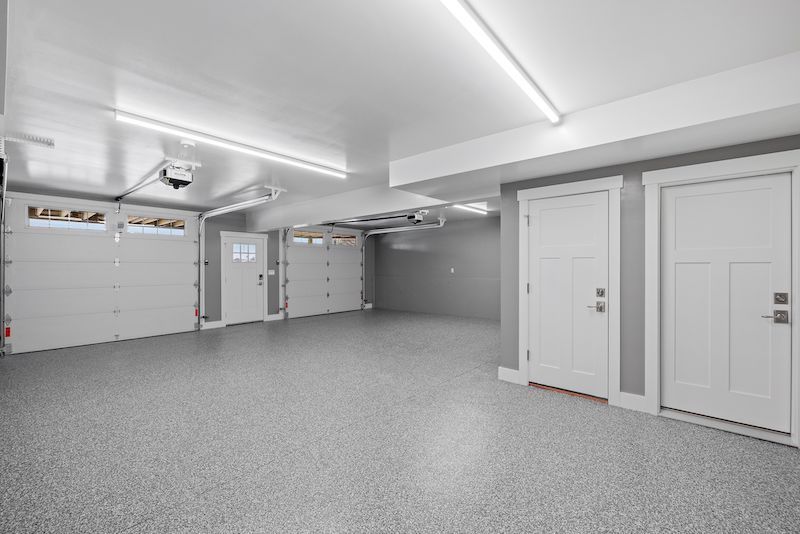
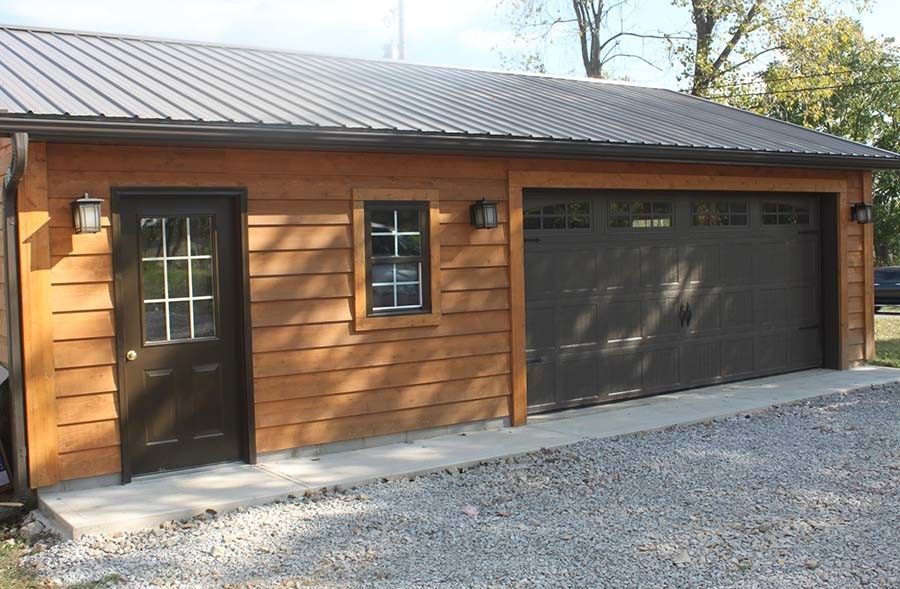
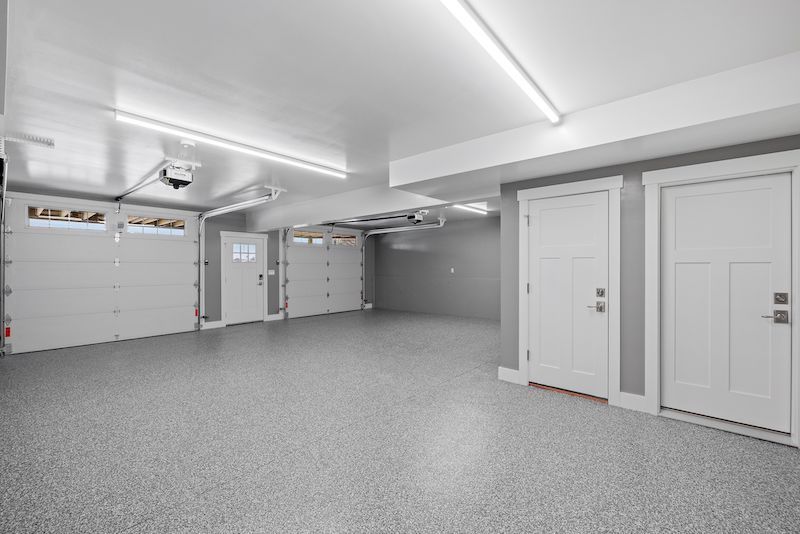